As the solar energy market
grows, asset owners and investors must understand the technical risks that can
emerge during project construction and impact the long-term operation and performance
of their assets. However, owners and investors – who are rightly focused on
project finance -- are not always well positioned to see these risks. Instead,
they are reliant upon an independent engineer, hired to diligence the project
through a desktop review of engineering and project documents, and one or two
site visits during construction. Meanwhile, engineering, procurement, and
construction (EPC) contractors are focused on project construction and the
immediate warranty period thereafter, with less focus on long-term performance.
As a result, while many EPC contractors build high quality assets, the owner
can still be faced with the long-term operational challenges that may emerge
once the warranty period expires.
This gap can result in lost
production, as well as increased operational expenses like maintenance costs.
Solar asset owners should encourage collaboration between their project
delivery and asset management teams, establishing precedent for them to work
together during and after construction to ensure that solar assets are built to
and perform at the expected standard. Over the past several years, Sol’s
delivery and asset management teams have been compiling a list of common issues
that can impact long-term solar project performance. We reviewed the punch
lists from approximately 50 projects – a combination of rooftop, ground mount
and carport projects - and identified five of the most prevalent issues we
encounter:
- Poor wire management: Every large PV system is home to thousands upon thousands of wires. Managing them correctly is of vital importance, yet many systems are prone to poor wiring. Photo 1a shows a site with various issues, including cables in tension, bend radius violations, and generally sloppy workmanship. Photo 1b shows cables and connectors on the surface of a roof. These poor practices can lead to safety and reliability issues such as premature insulation failures and electrical arcing and, in the worst case, fires. The contractor was required to redo the wire management in both instances. Proper wire management is indicative of high-quality workmanship; it is among the most visible aspects of a solar project, and among the most important practices a contractor can undertake.
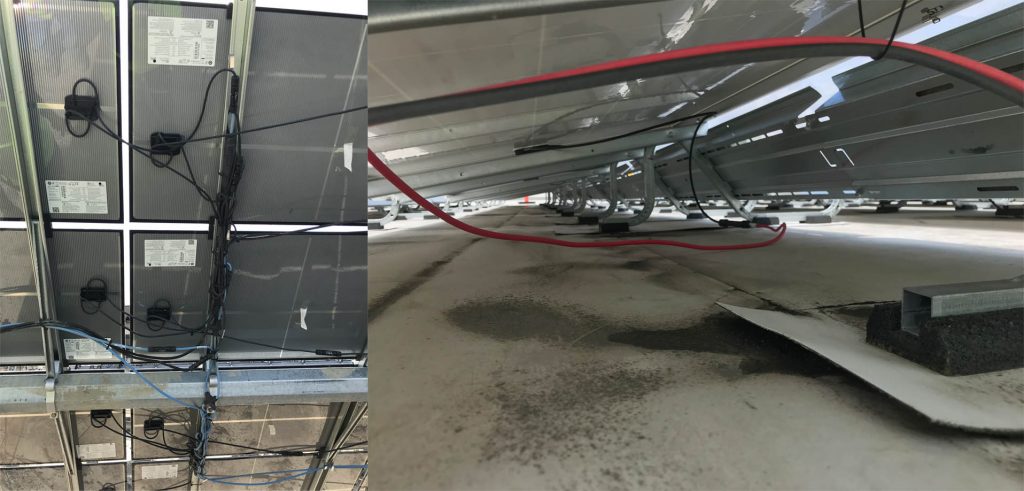
- Improperly installed PV connectors: As with cables, every project has thousands of electrical connections which allow for the proper flow of generated power. As seen in photos 2a and 2b, connectors can often be an overlooked area of construction where mistakes are made. 1a shows a mated pair where the male and the female connectors are from different manufacturers, while 1b shows a connector where the nut on the left side is not torqued down properly, as seen by the three visible threads. Both issues can lead to problems like increased heat and resistance and electrical arcing issues, as well as potential UL listing violations. Manufacturer-specific installation instructions are key. These issues may not be noticed by untrained eyes but can have long-term impacts. If an asset owner is considering selling their PV plants, a savvy potential buyer may note these issues and demand remediation or a reduction in sale price.

- Improperly installed weather station components: Irradiance and temperature are key inputs to determining the performance of a solar project. These are measured with devices called pyranometers and back-of-module temperature sensors. Photo 3a shows a module temperature sensor affixed to the space in between the cells, rather than the best practice location in the center of the cell near the center of the module. Photo 3b shows an irradiance sensor installed right next to a shiny pole, which can cast a shadow or reflections at different times of the day. Both of these issues lead to poor data quality and can cause asset owners to come to misleading conclusions about project performance.
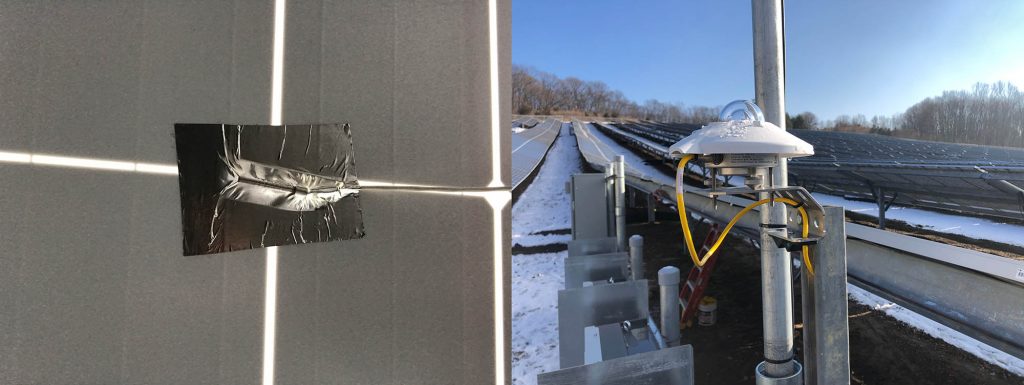
- Civil construction and design issues: Ground mounted solar projects often require preparation work to prepare the site for long term use as the site for a solar project. Issues can arise from poor grading and poor erosion control practices. Grading, evening out topography on site, can aid in effective storm water draining from the site. In addition, if erosion is occurring onsite, it can impact the structural integrity of the racking system, expose buried cable, and prevent long term growth of grass or groundcover designed to stabilize the soil post construction.
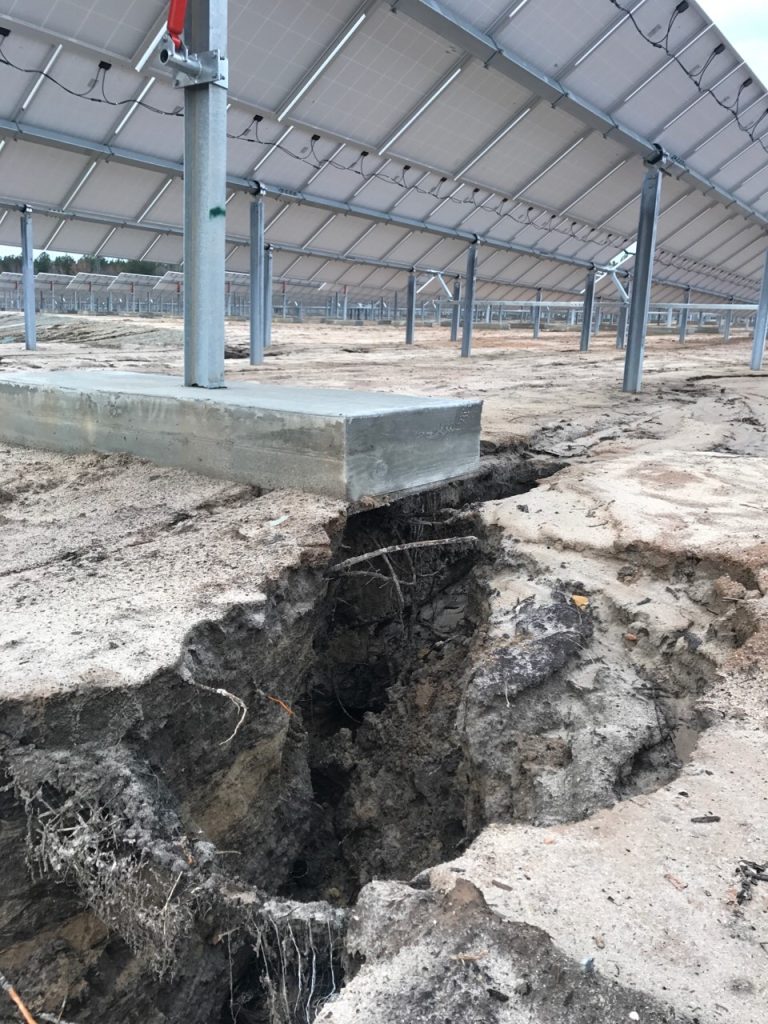
- Data Acquisition Systems (DAS) and Remote Monitoring: PV project owners and O&M service providers can monitor the performance of the sites and components through cloud-based software known as DAS. Though we’ve noted many common issues with data acquisitions system hardware, a thorough audit of the system in the online portal (as well as energy, power factors, etc.) can uncover a variety of problems, including mislabeled equipment, scaling issues with voltages and currents, missing data, sensor problems, and underperformance. Photo 5 shows a series of similarly sized string inverters which should be producing about the same energy. Proper setup of the system in these online portals is crucial for accurate data reporting.
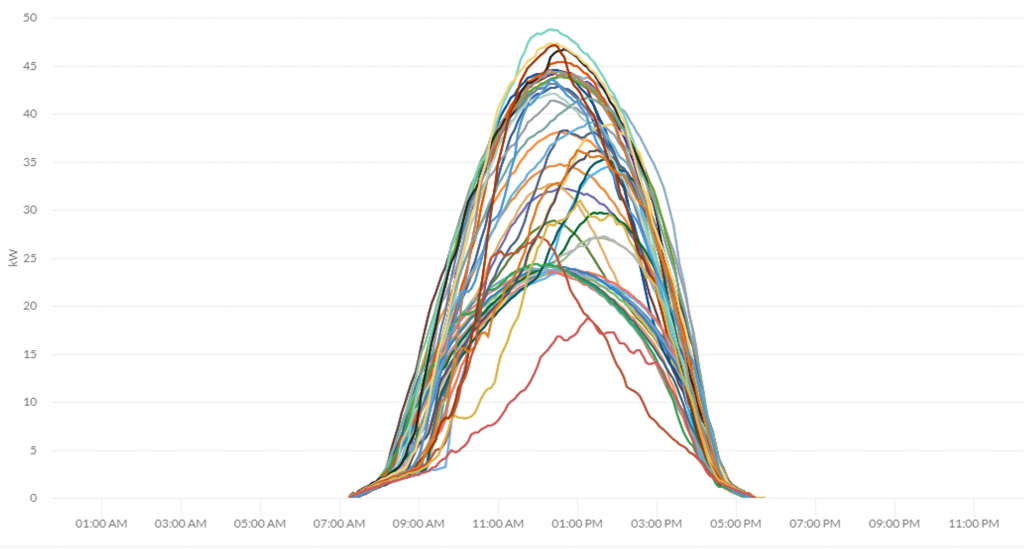
Post Construction
As projects reach the testing
and commissioning phase, it is imperative that project managers engage their
asset management team to review commissioning reports, work with in-field
construction managers on punch lists, and review the capacity testing to ensure
performance. Collaborating on these post construction efforts helps inform both
project and construction manager efforts to close out projects while providing
the performance engineering team with valuable context around a plant’s early
operation. Such information can help reduce downtime in the early stages of
operation.
Beyond construction-specific
activities, the asset management and delivery teams should regularly
collaborate to the benefit of the company’s projects. At Sol, this
collaboration includes quarterly reporting on asset performance and regular
technical specifications updates. This reporting enables us to collect and
share feedback from different stages of the construction and operations process
to ensure the project’s success.
Through collaboration, a solar asset owner’s project managers and asset managers can identify potential issues early on and apply lessons learned to protect long term investments and returns. These efforts: reviewing prior punch lists to see trends, collaborating on commissioning activities, and meetings regularly to report on performance, combine the knowledge of project managers and asset managers, ultimately leading to a higher quality solar asset and a stronger return on solar project investments.
ABOUT
SOL SYSTEMS
Sol
Systems is a leading national solar energy firm with an established reputation
for integrity and reliability across its development, infrastructure and
environmental commodity businesses.To date, Sol has developed and/or
financed over 850 MW of solar projects valued at more than $1 billion for
Fortune 100 companies, municipalities, counties, utilities, universities and
schools. The company also actively shapes and trades in environmental commodity
and electricity markets throughout the United States. The company was founded
in 2008, is based in Washington D.C, and is led by its founder. Sol Systems
works with its team, partners, and clients to create a more sustainable future
we can all believe in. For more information: www.solsystems.com